
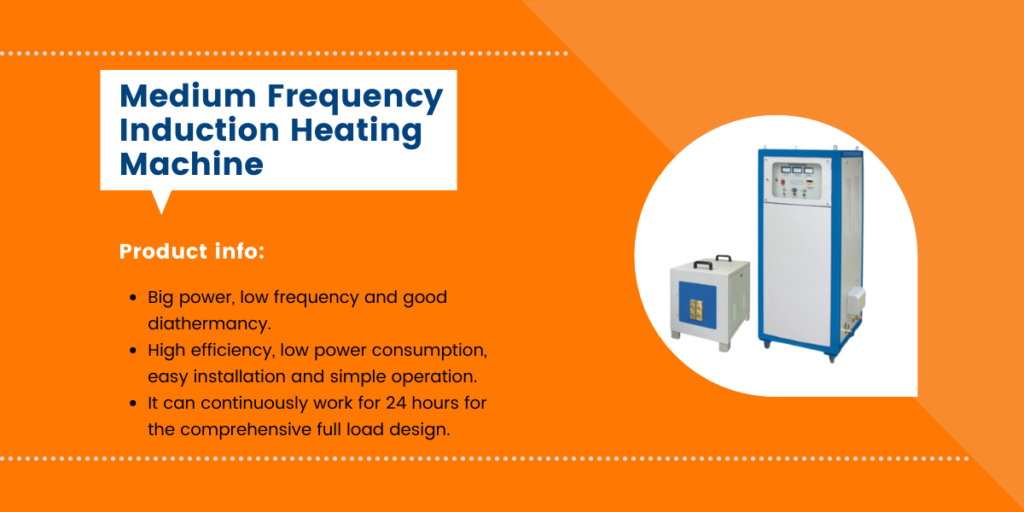
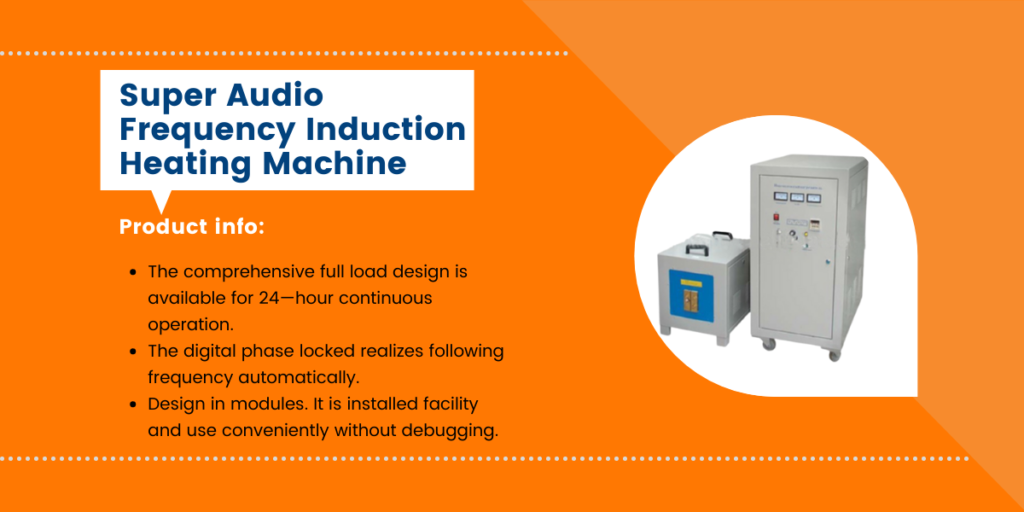
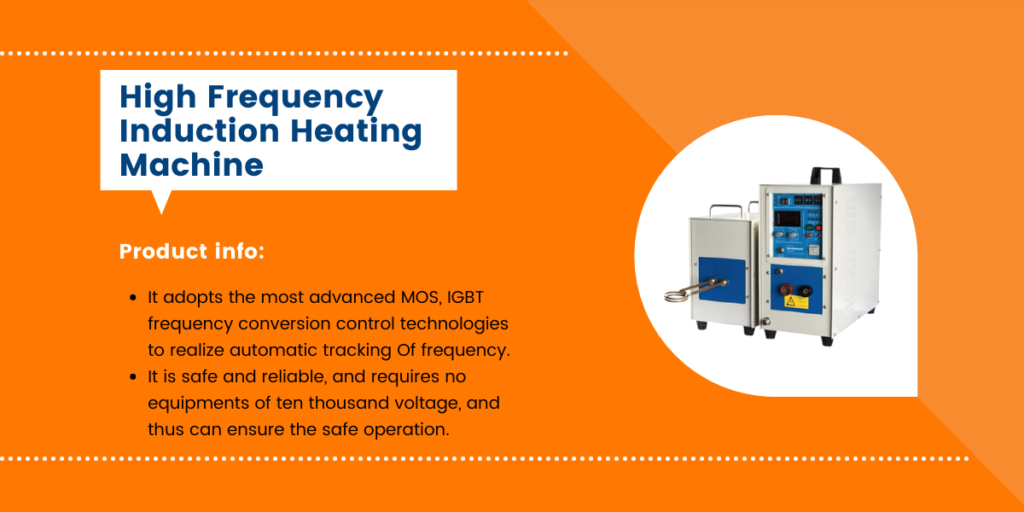
Induction forging Machine is a specialized system which is used to heat metal billets or work pieces to a certain temperature and then give them shape by means of flame forging. This instruction makes use of a heating technique, where the metal is heated by a beam without direct contact to the field of an electric magnet.
The rare properties of providing continued heat provide an example for their high-scale production and application in a world where there is growing demand for physical and chemical weapons.
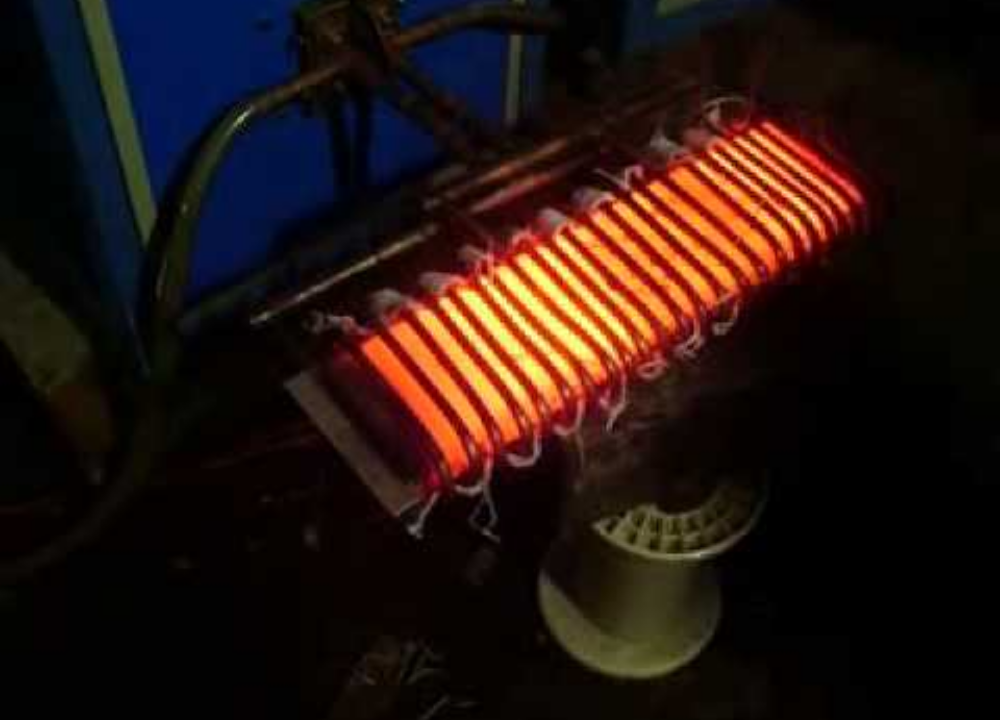
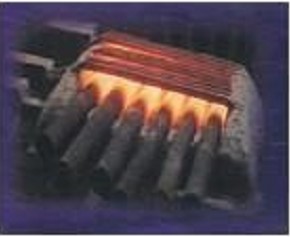
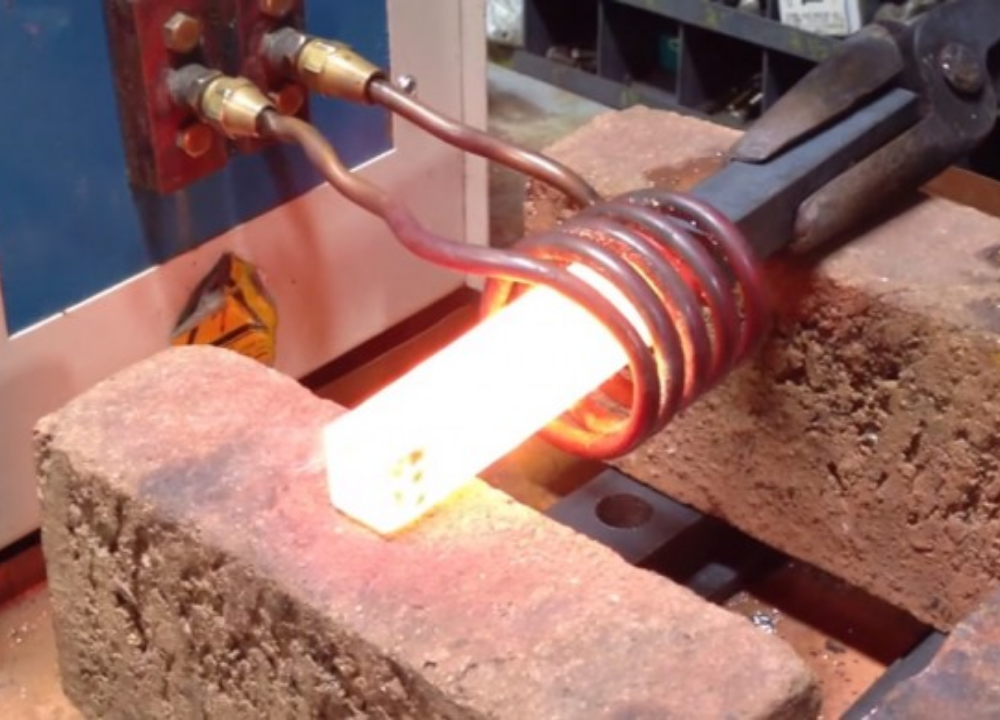
Best Overview Induction Forging Machine
Hot forming, hot forging, diathermy molding, hot rolling, hot upsetting and red stamping are all used induction heating machine to make the work-piece nearly have the same temperature on surface and internal, then puching into required shape, which mainly adopt electromagnetic induction and heat conduction principle.
Main Features
1. Fast Heating : The quickest rate of heating is less than 1 second, and the rate of heating is available for adjustment and control.
2. Widely Applicable : it can be used to heat various metal parts(can replace the removable induction coil for different shape).
3. Low Power Consumption :
as compared with traditional vacuum tube high frequency machine, the heat efficiency can be over 95%.
4. High Effectiveness : it is applicable to control the temperature for heating work pieces that it has such features as uniform heating, fast warming and limited oxic horizon.
5. High Efficienc : it can work continuously for 24 hours for comprehension full load design. and with the function of automatic setup, just one person can operate it that can save the process.
6. Small size and light weight : it has a weight of only several dozens of KGS and with small size that can save the space of the workshop and can be moved conveniently.
7. Easy operation : CNC design, easy installation and simple operation that you can learn to operate it within several minutes. It can be started to perform heating operation on condition that water and power supply is available.
8. Environmental Protection : it is free of any noise, exhaust gas and dust that can provide a much better environment for the workers than the conventional heating with such fuels as coal, gases, and oil.
Application
Fasteners, hardware tools, automobile and motercycle accessories, rigging, pipe fittings, twist drill, atlas, table, mould parts, standard parts, handicrafts, machinery parts, brass lock, lock, rivets and other hardware and metal accessories.
Model and Frequency Selection
Power determines the work-piece heating speed, frequency determines the work-piece temperature difference between inside and outside.
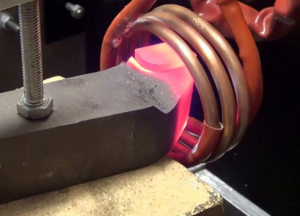

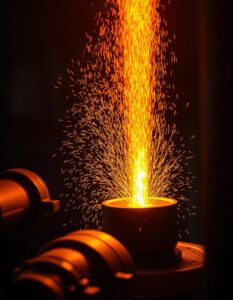
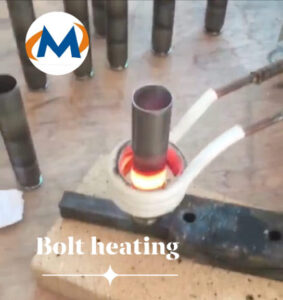
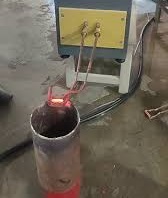

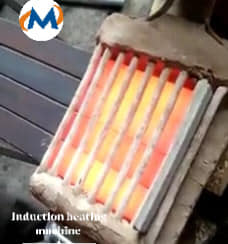
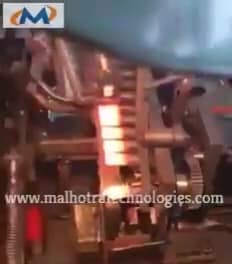
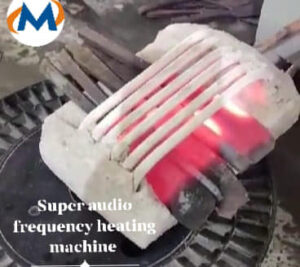
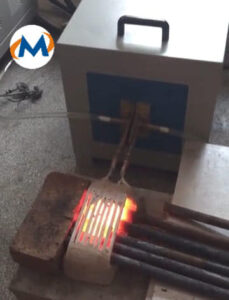
Special Fasteners Forging Machine
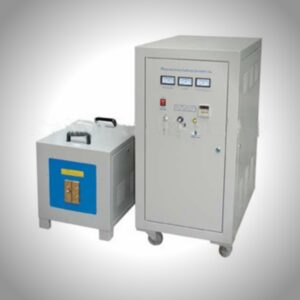
Super Audio Frequency Series
MTC-30KW
MTC-50KW
MTC-60KW
MTC-80KW
MTC-120KW
MTC-160-KW
MTC-200KW
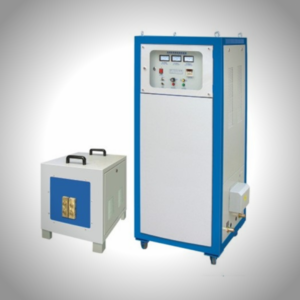
Medium Frequency Series
MTZ-15KW
MTZ-25KW
MTZ-35KW
MTZ-45KW
MTZ-70KW
MTZ-90KW
MTZ-110KW
Who Are We
Malhotra Technologies Established in 2007, Malhotra Technologies (INDUCTION MASTER) is a reputed company that manufactures and supplies a broad assortment of (INDUCTION HEATING MACHINE) induction-hardening machines,Induction Forging Machine, high-frequency induction heaters, medium-frequency power heaters, UHF induction heaters, super Audio Frequency machine, annealing machine, sintering machine, electroplating rectifiers, heat-treatment machine, and brazing machine. They also supply products like 15 series induction heaters, 25 series induction heaters, 35 series induction heaters, 70 series induction heaters, medium frequency power heaters, melting machine frequency power heaters,s and forging furnace frequency power heaters. These items are developed using high-quality raw materials procured from retailers following international norms. KNOW MORE.
Malhotra Technologies 25 years professional manufacturing industries company.
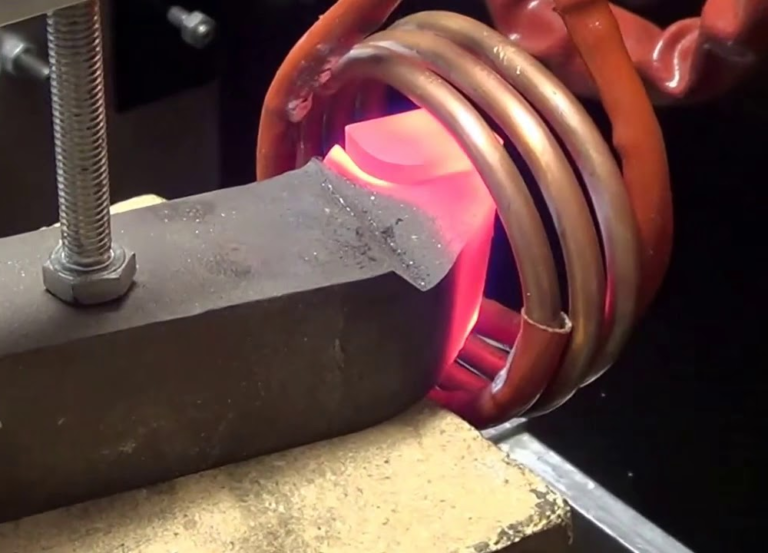
Induction Heating Mahine For Forging
Induction Heating Machines for forging are a modern solution in modern metal science, proposing a safe, efficient and environmentally friendly way to heat metals. Instead of traditional methods such as gas or radiant heating, infrared heating uses electric steam energy to generate heat in see-through furnaces. This Technology has transformed industries such as automotive, aerospace and oil and gas by providing faster, more energy-efficient and more controlled heating of furnace systems. This article sheds light on the principles, developments, applications and future trends of index heating machines that are used in the furnace industry.